The study of naval architecture deals with the design and construction of ships, offshore and marine structures, equipment and systems to survive and operate in marine environment. A naval architect is an engineer with a working knowledge of ship hydrodynamics and ship systems and a basic understanding of offshore structures and systems design.
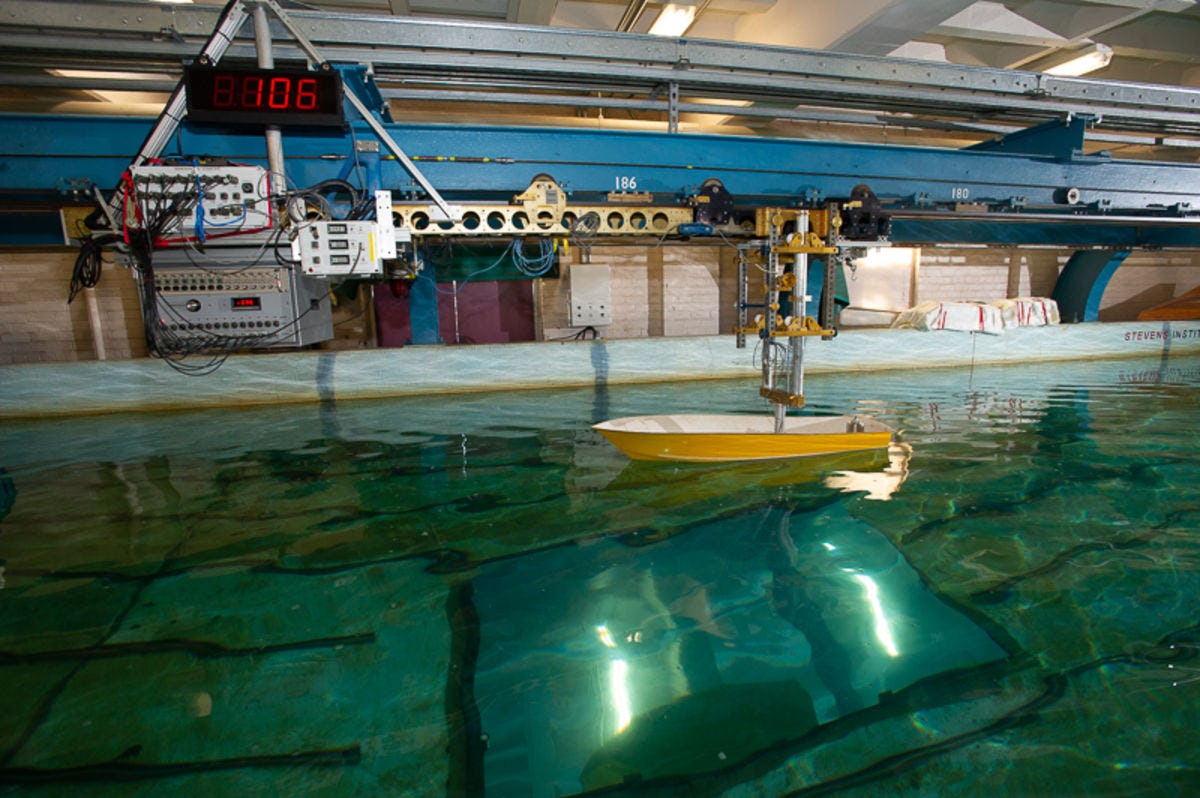
Resistance, powering, seakeeping, maneuvering and stability are the key issues in the field of naval architecture. A combination of physical model studies and computational fluid dynamics is ideal for advancements in the field.
At Davidson Laboratory, the main research focus is on high-speed marine craft. Current projects involve development of database and eventual ship design tool using archived towing tank data, development of an active ride control system to improve seakeeping performance of high-speed vessels and development of better hullforms, passive/active controls to reduce the wake wash generated by high-speed ferries. The Davidson Laboratory also uses computational tools to study and optimize hull and appendage designs.
Ship Models
Model testing is done to determine the behavior of vessels at full scale without the expense of actually building the real vessel until the design is proven on a small scale. Model building is several thousand years old, as models are known to have been used and tested in Egypt. Today, computer simulation supplements physical models, but computer models are insufficiently reliable and a priori correct to be used without careful calibration against reality. Thus even when computer models are used, usually a physical model is built, and the computer model is carefully calibrated from the physical one.
Terminology
Before discussing how testing models works, first we must define the terminology. The scale of a model is usually expressed as the ratio of the length of the envisioned ship divided by the length of the model and is denoted by l (lambda). The width of a ship at its widest point is called itsbeam, the depth is called the draft. All three of these quantities are scaled down for a model in the same way, so that the model is the same shape as the full-scale vessel, only smaller. When scaling a model up by a factor of 10, its total mass or displacement increases by a factor of 1000 (103). Resistance is the drag on the ship from all sources, which determines how fast a ship can move for a given power input. Effective Horsepower (EHP) is the amount of power that must be delivered in order to move the ship at a design speed. Effective horsepower is not the same as real engine horsepower, because of losses in the transmission, and most importantly, at the propeller. In practice, real horsepower must be approximately twice EHP in order for the ship to move at the design speed.
For all variables relating to the full-scale ship, we use the subscript s. For all variables relating to the model, we use the subscript m. The resistance of a vessel moving through water also depends on the physical characteristics of the water. Salinity, and to a lesser extent, temperature, affect these properties. Some of the physical constants required include the density of the water in which the model is tested,rm=1.936 slugs/ft3, the density of standard seawater rs=1.9905 slugs/ft3 and the kinematic viscosity of water &num=1.0245e-5 ft2/sec,us=1.2791e- 5ft2/sec .
The scale of a model is defined as the length of the intended vessel, or "prototype vessel" divided by the length of the model.
The closer the model is to full scale, the more accurate the results, and also, of course, the more expensive the model is since it must be bigger. Generally, we test boats in the 60 foot range at a 10:1 scale.
Ship Resistance
Ship resistance can be broken up into four distinct types:
Frictional resistance, due to the motion of the hull through a viscous fluid.
Eddy resistance, due to the energy shed as eddies spin off the hull and particularly appendages.
Air resistance experienced by the above-water part of the hull. This component is usually quite small as air is 1000 times less dense than water, but particularly for high-speed craft it may be significant.
Wave-making resistance, caused by the variable pressure on the ship's hull and subsequent wave train.
For model scaling, we generally ignore air resistance, and lump the viscous friction and turbulent friction into a coefficient of friction, which is estimated with an empirical formula. At typical ship speeds, eddy resistance is dominant over viscosity because of the high Reynold's number. This friction term is proportional to the area of wall in contact with the water, the so-called wetted surface.
Wave making resistance, the other big component, is caused by moving a hull through the water creates a high pressure region at the bow (creating a bow wave), and a smaller high pressure wave at the stern, and lower pressure (and corresponding depression) along the sides of the boat. The wave then propagates away from the hull. Wave-making is proportional to the displacement of a vessel.
Scaling
The two sources of ship resistance do not scale the same way. The displacement of a vessel scales according to L3, while its wetted area increases with L2. Thus for a model which is scaled down by identical factors of length, beam (width) and draft (depth) skin friction is actually larger relative to the model by a factor of lambda. This means that in order to scale down a model and test the equivalent skin friction, the model must be run through the water faster than the full-scale ship by a factor of lambda. For a 10:1 scale model where the full-scale ship is to move at 30 knots, this means that the model must be tested at 300 knots which is completely impractical.
The wave-making resistance, on the other hand, scales with square root of lambda. For a model at 1:10 scale for the same 30 knot design speed above, the speed at which the model must be run is 30/&radic 10 = 9.48 knots. Since this is reasonable, we run model tests at this speed, and estimate the frictional resistance empirically.
The algorithm for computing the effective horsepower (EHP) required to drive a ship at versus in order to predict the amount of power needed to move a ship at a certain speed, we first must compute the total resistance of the ship at that speed. That in turn depends on the friction resistance (which we can estimate analytically) and the wave-making resistance. We measure total resistance on a model, estimate skin friction, subtract it to compute wave-making resistance for the model, then scale up the wave-making resistance to ship scale, estimate friction at full scale, and compute the total resistance for the ship.
Again, EHP is not the power required of the engine. In practice, losses in the transmission — particularly at the propeller — mean that approximately twice as much power is required in order to achieve the EHP at the design speed.
The inputs for a model are listed in the following table:
Variable | Description |
VM | Velocity of the model |
RM | Resistance of the model |
WLM | Waterline Length of the model |
WAM | Wetted Area of the model |
λ | Scale factor |
ρ m | Density of water in the test tank |
υ m | Viscosity of water in the test tank |
ρ s | Density of water at sea |
υ s | Viscosity of sea water |